Welcome to our comprehensive guide on how to repair cracks in concrete in New Zealand. Whether it’s your driveway, patio, or foundation, concrete cracks are a common issue due to New Zealand’s unique weather conditions and natural ground movements. Repairing these cracks early is essential to maintaining the structural integrity of your concrete and preventing further damage. In this guide, we’ll walk you through the causes of concrete cracks, how to assess their severity and provide easy-to-follow steps to help you fix them yourself, ensuring a long-lasting repair that stands up to New Zealand’s climate.
To repair cracks in concrete in New Zealand, start by cleaning the cracks to remove debris and dirt. For small hairline cracks, use a liquid filler or crack sealer, while larger cracks may require a concrete patch or epoxy injection. After applying the repair material, smooth the surface and allow it to cure properly. Prevent future cracks by sealing the concrete and ensuring proper drainage to reduce water infiltration. Regular maintenance and timely repairs can extend the life of your concrete surfaces.
- Common Causes Of Concrete Cracks In NZ
- Assessing The Severity Of Concrete Cracks
- Tools And Materials You Will Need
- Preparing The Crack For Repair
- How To Repair Different Types Of Concrete Cracks
- Curing And Finishing The Repair
- Preventing Future Cracks
- When To Call A Professional
- Eco-Friendly Concrete Repair Solutions
- FAQs: About How To Repair Cracks In Concrete NZ
- Conclusion
Common Causes Of Concrete Cracks In NZ
Concrete cracking is a common issue that can affect the durability and appearance of both residential and commercial structures. In New Zealand, specific environmental factors and installation practices play a significant role in why concrete may crack prematurely. Understanding the root causes can help homeowners and businesses take preventive measures to avoid costly repairs. Let’s dive into the most common reasons why concrete cracks in NZ.
Climate Considerations
New Zealand’s unique and variable climate significantly impacts the lifespan of concrete. The country experiences a range of weather conditions that can lead to concrete cracking, primarily due to:
- Rainfall: Excessive moisture from heavy rainfall can infiltrate the concrete, causing expansion. If water penetrates the concrete surface and later evaporates, it can leave behind cracks as the structure shrinks. Poor drainage or exposure to long periods of wet weather also weakens the concrete over time.
- Freeze-Thaw Cycles: In colder regions of New Zealand, such as the South Island, freeze-thaw cycles are a frequent issue. Water seeps into small pores in the concrete. When temperatures drop, the water freezes and expands, creating internal pressure that eventually leads to cracks. Repeated freezing and thawing over time can severely damage the integrity of the concrete.
- Humidity and Heat: In areas with fluctuating temperatures and high humidity, concrete expands and contracts. This thermal movement causes stress within the concrete, especially when exposed to extreme heat during the summer months. Without proper expansion joints, this natural expansion can lead to cracking.
Natural Ground Movements
New Zealand’s geological landscape is another key factor contributing to concrete cracks. As the country sits on active tectonic plates, seismic activity and ground movements are constant concerns.
- Seismic Activity: Earthquakes, both large and small, create shifts in the earth that directly impact any concrete structure. Even minor tremors can cause hairline cracks, which may grow over time with subsequent movements. Larger seismic events can lead to significant structural damage, where concrete cracks can compromise the stability of buildings or roads. Learn more about New Zealand’s seismic activity and earthquake risks from GeoNet.
- Soil Shifting: Different types of soils expand and contract due to moisture variations, leading to uneven settlement beneath the concrete. This is especially common in areas prone to clay soil. As the ground beneath shifts, it causes the concrete above to move, resulting in visible cracking on the surface.
- Settlement: Over time, the natural settling of the ground can create voids beneath concrete slabs. Without adequate support, the concrete may sink or become uneven, resulting in cracks that may widen as the structure continues to shift.
Poor Installation or Materials
Even under ideal conditions, the quality of the installation process and the materials used are crucial in preventing concrete cracks. Some common issues include:
- Improper Mixing: Concrete must be mixed to precise ratios of water, cement, and aggregates to achieve optimal strength. Too much water weakens the concrete, making it more prone to cracking as it dries and cures. On the other hand, a mixture that is too dry can lead to poor bonding and early failure.
- Inadequate Curing: Curing is a vital process where concrete is kept moist after being poured, allowing it to reach maximum strength. When concrete is not properly cured, it may dry out too quickly, leading to surface cracks. In New Zealand’s windy or hot conditions, rapid moisture loss can occur if the concrete is not adequately protected during the curing period.
- Subpar Application Techniques: Inexperienced contractors or rushed construction processes often result in weak points in the concrete. Issues like insufficient reinforcement, uneven surfaces, or poorly prepared ground bases can cause cracks to form soon after installation. Additionally, the lack of control joints or improperly spaced joints can lead to random cracking as the concrete expands and contracts over time.
Concrete cracking is a common concern in New Zealand due to a variety of environmental and structural factors. From the country’s unpredictable weather to natural ground movements and even human error during installation, each factor contributes to the overall vulnerability of concrete structures. However, by understanding these causes and addressing them proactively, you can extend the life of your concrete and prevent unsightly or dangerous cracks from forming.
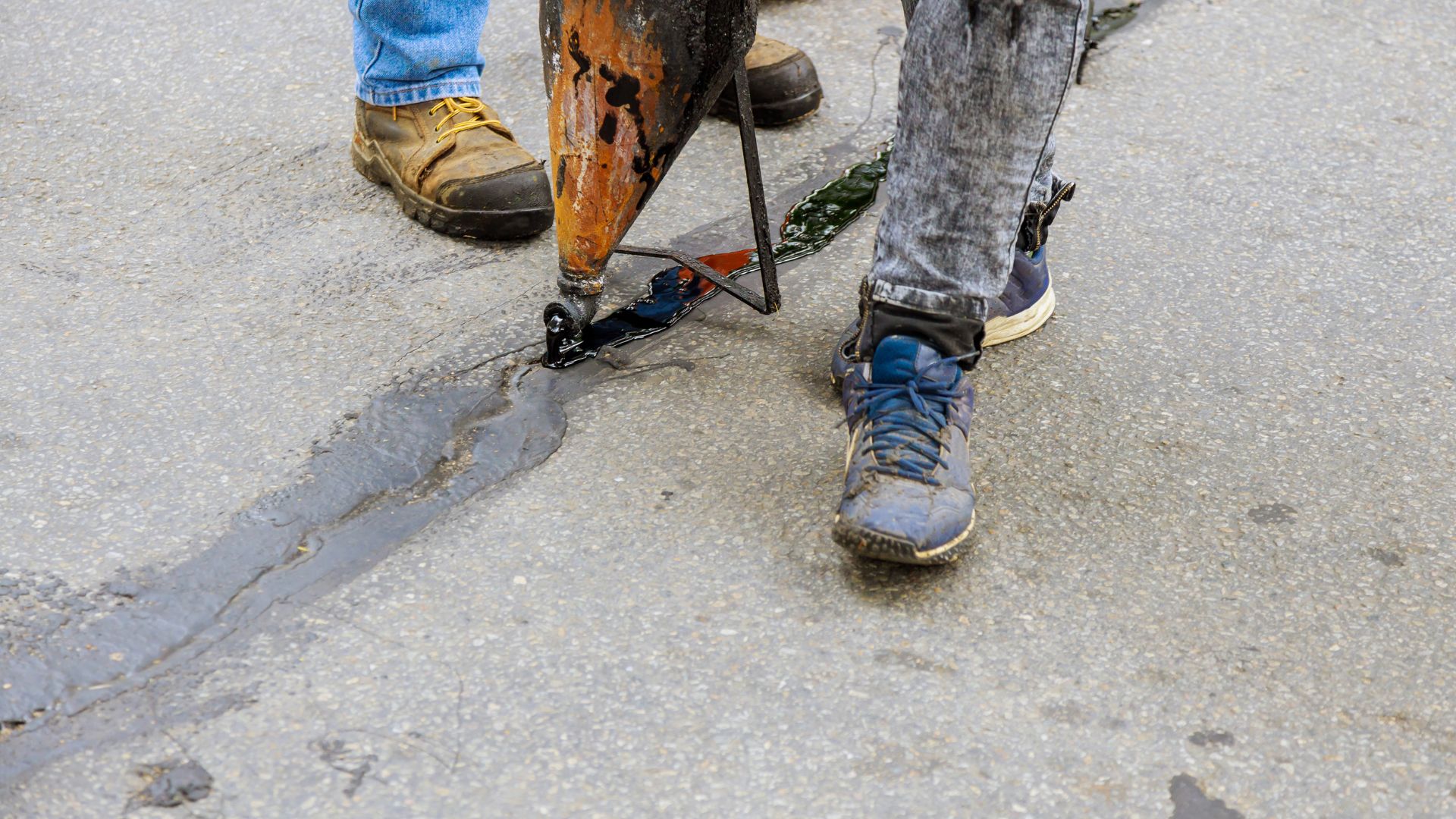
Assessing The Severity Of Concrete Cracks
Concrete cracks are a common occurrence in both residential and commercial structures, but not all cracks are created equal. Properly assessing the severity of these cracks is crucial in determining whether immediate repair is necessary, or if they are minor enough to be handled over time. Understanding the types of cracks and knowing when it’s time to call in a professional can help you save both time and money while ensuring the structural integrity of your property.
Types of Cracks in Concrete
Concrete cracks can be classified into different categories, each with unique characteristics that indicate their potential cause and level of severity. Here’s a breakdown of the most common types:
Hairline Cracks
Hairline cracks are thin, shallow cracks that usually appear in the surface layer of concrete. They are often a result of concrete shrinking during the curing process. While they may not initially seem like a cause for concern, if left unchecked, hairline cracks can allow moisture to seep into the concrete, potentially leading to more significant damage over time.
Shrinkage Cracks
Shrinkage cracks develop as concrete dries and cures. These are typically non-structural and occur when the surface layer shrinks faster than the inner layer. Shrinkage cracks are usually harmless, especially when they appear early in the curing process. However, excessive cracking could indicate improper concrete mix or drying conditions.
Structural Cracks
Structural cracks are more serious and often signal a problem with the foundation or load-bearing aspects of the structure. These cracks are typically wider than hairline cracks and may appear in patterns that suggest movement or shifting. Common causes include soil settlement, heavy loads, or seismic activity. Structural cracks can compromise the integrity of the building and should be addressed immediately by a professional.
Settlement Cracks
Settlement cracks form when the ground beneath the concrete settles unevenly, causing the slab to crack under the shifting pressure. These cracks can vary in size and severity, depending on the amount of movement occurring in the underlying soil. Like structural cracks, settlement cracks may require professional evaluation to determine if there are deeper foundation issues at play.
Expansion Cracks
Concrete expands and contracts with temperature fluctuations. Expansion cracks occur when the concrete expands but lacks enough room to accommodate the movement, causing it to crack under the pressure. Expansion joints are typically used to prevent these types of cracks, but when they fail or are improperly installed, expansion cracks can form.
When to DIY vs. Call a Professional
Knowing when to tackle a concrete crack repair on your own and when to call a professional can be tricky, but there are a few key factors to consider:
Size and Width of the Crack
- DIY: Hairline cracks or cracks less than 1/8 inch wide are usually safe to fix yourself. These can often be addressed with simple DIY solutions like concrete filler, sealant, or patch kits. Ensure that you clean out the crack thoroughly before applying any product.
- Call a Professional: Cracks wider than 1/8 inch, especially those that are increasing in size over time, should be assessed by a professional. Large cracks could indicate deeper issues with the foundation or structural support of the building, which may require more extensive repairs or reinforcement.
Location of the Crack
- DIY: Cracks in non-load-bearing areas like patios, driveways, or sidewalks are usually suitable for DIY repairs, as they do not typically affect the structural integrity of the building. A concrete patch or crack sealant can often resolve the issue.
- Call a Professional: Cracks in load-bearing walls, beams, or columns are a sign of structural damage and should be examined by a professional immediately. These areas are critical to the stability of the building, and improper repair could lead to dangerous conditions or further damage.
Cause of the Crack
- DIY: If the crack is the result of natural shrinkage or surface wear, it’s likely safe to repair on your own. These types of cracks are common and don’t generally indicate deeper issues.
- Call a Professional: Cracks caused by soil settlement, poor drainage, or foundation movement should be investigated by an expert. These underlying problems can lead to significant structural damage if not addressed properly, and DIY fixes may only serve as temporary solutions.
Movement and Progression
- DIY: Static cracks that aren’t growing or shifting over time can often be repaired with a DIY approach. Monitoring the crack to ensure that it remains stable is important, but as long as there is no significant movement, DIY repairs should suffice.
- Call a Professional: If the crack is continuing to grow or if you notice signs of movement (such as uneven floors, doors sticking, or new cracks appearing), it’s best to call in a professional. Progressive cracks indicate that something is shifting within the structure, which requires expert intervention.
Assessing the severity of concrete cracks involves a careful look at the type, size, and cause of the crack, as well as its location and progression. While minor cracks can often be addressed with DIY repairs, larger or more complex cracks may require professional evaluation to ensure the long-term stability of your structure. By staying proactive and addressing cracks early, you can prevent more significant problems down the road and maintain the integrity of your property.
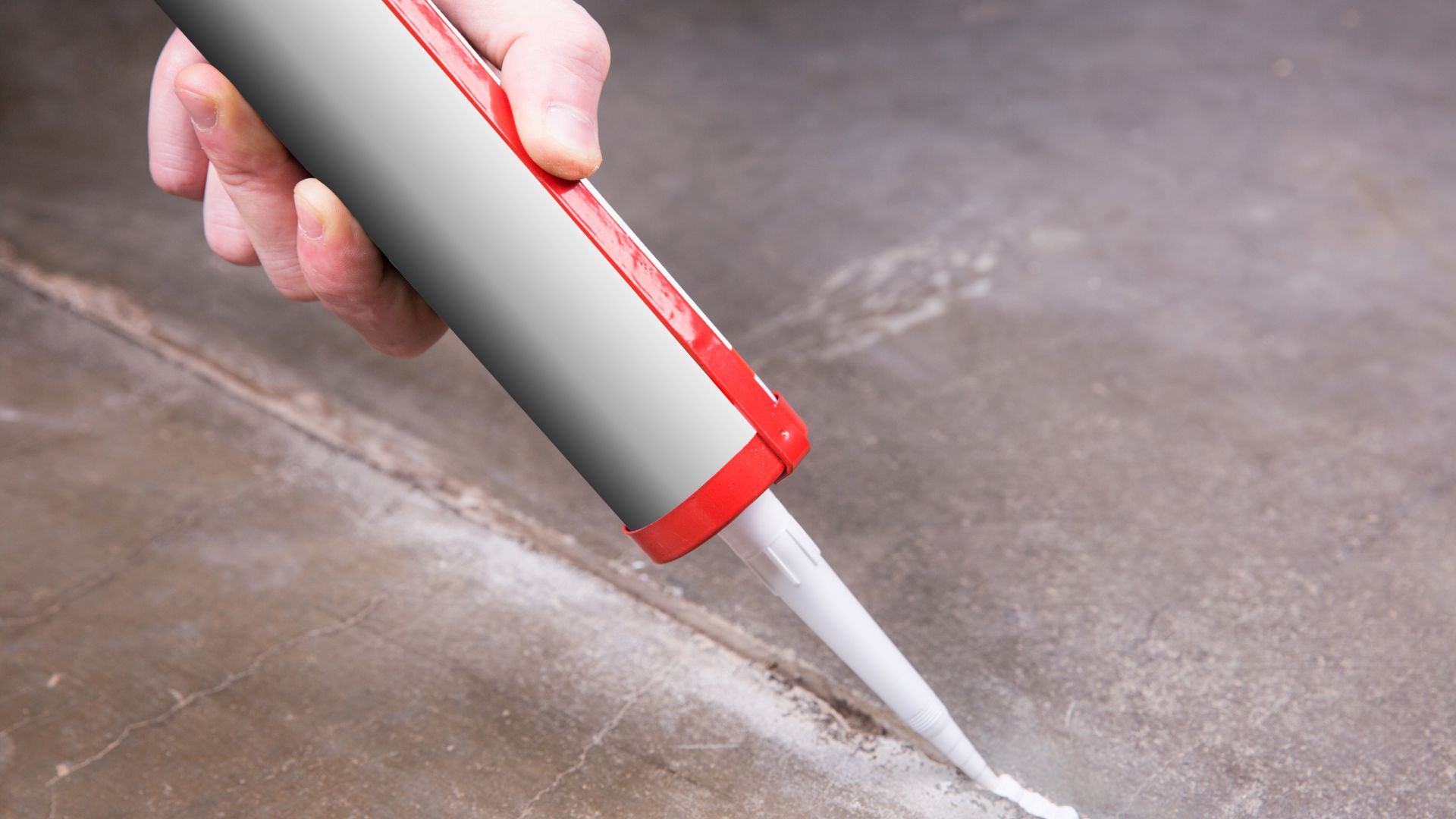
Tools And Materials You Will Need
When tackling a concrete repair project, having the right tools and materials on hand is crucial to ensure the job is done efficiently and effectively. Here’s a breakdown of what you’ll need to complete your repair successfully:
Basic Tools
To start, you’ll need a few essential tools that are likely already in your toolbox or easily available at a hardware store. These include:
- Wire Brush: This is used to clean out the crack and remove loose debris, dust, or old patch materials before beginning the repair. Proper surface preparation is key to ensuring a lasting repair.
- Hammer and Cold Chisel: For more stubborn debris or to widen the crack to allow for better material adhesion, a hammer and cold chisel come in handy. Gently tapping the chisel into the crack helps create a clean and workable area.
- Putty Knife: A putty knife is essential for applying patch materials smoothly and evenly. This ensures a neat finish and helps to properly seal the crack or damaged area.
Repair Materials
Choosing the correct repair material is critical to achieving a long-lasting fix. The material you select should depend on the type and size of the crack you’re dealing with, as well as the environment (indoors, outdoors, load-bearing, etc.). Here’s a breakdown of the most commonly used repair materials:
- Concrete Patch: This is typically a pre-mixed compound designed specifically for filling in cracks and small holes in concrete. It’s a great option for minor damage and surface-level cracks.
- Epoxy: Epoxy resin is a highly durable material that’s perfect for larger, structural cracks. It provides strong adhesion and is often used for cracks that need reinforcement or will bear weight.
- Polyurethane Sealant: If you’re dealing with hairline cracks or areas prone to movement (like driveways or sidewalks), polyurethane sealant is flexible enough to handle shifts without cracking again. It’s waterproof and ideal for outdoor use.
Choosing the right material is vital. For hairline cracks, polyurethane sealant may be all you need, but for deeper structural issues, epoxy or concrete patch might be more appropriate. Always read the product specifications and choose based on the crack’s depth, width, and location.
Protective Gear
Safety should always be a top priority when working with concrete repair materials. While the work might not seem particularly hazardous, dealing with chemicals, dust, and sharp tools can pose risks. Be sure to use:
- Gloves: Protect your hands from chemicals, rough surfaces, and sharp tools. Some repair materials, like epoxy and concrete patches, can be harsh on the skin, so wearing gloves is non-negotiable.
- Safety Glasses: Anytime you’re chiseling, mixing, or dealing with dust or debris, eye protection is essential. Flying debris or splashes from repair materials can easily cause injury if your eyes are unprotected.
- Dust Mask: Concrete dust can be harmful if inhaled, especially when chiseling or using a wire brush. Wearing a dust mask helps prevent respiratory irritation and long-term health issues.
By gathering the right tools, selecting appropriate repair materials, and prioritizing safety with proper protective gear, you’ll be well-equipped to handle concrete repairs efficiently and safely. Taking these steps ensures a smoother process and a more professional result, no matter the size or scope of your project.
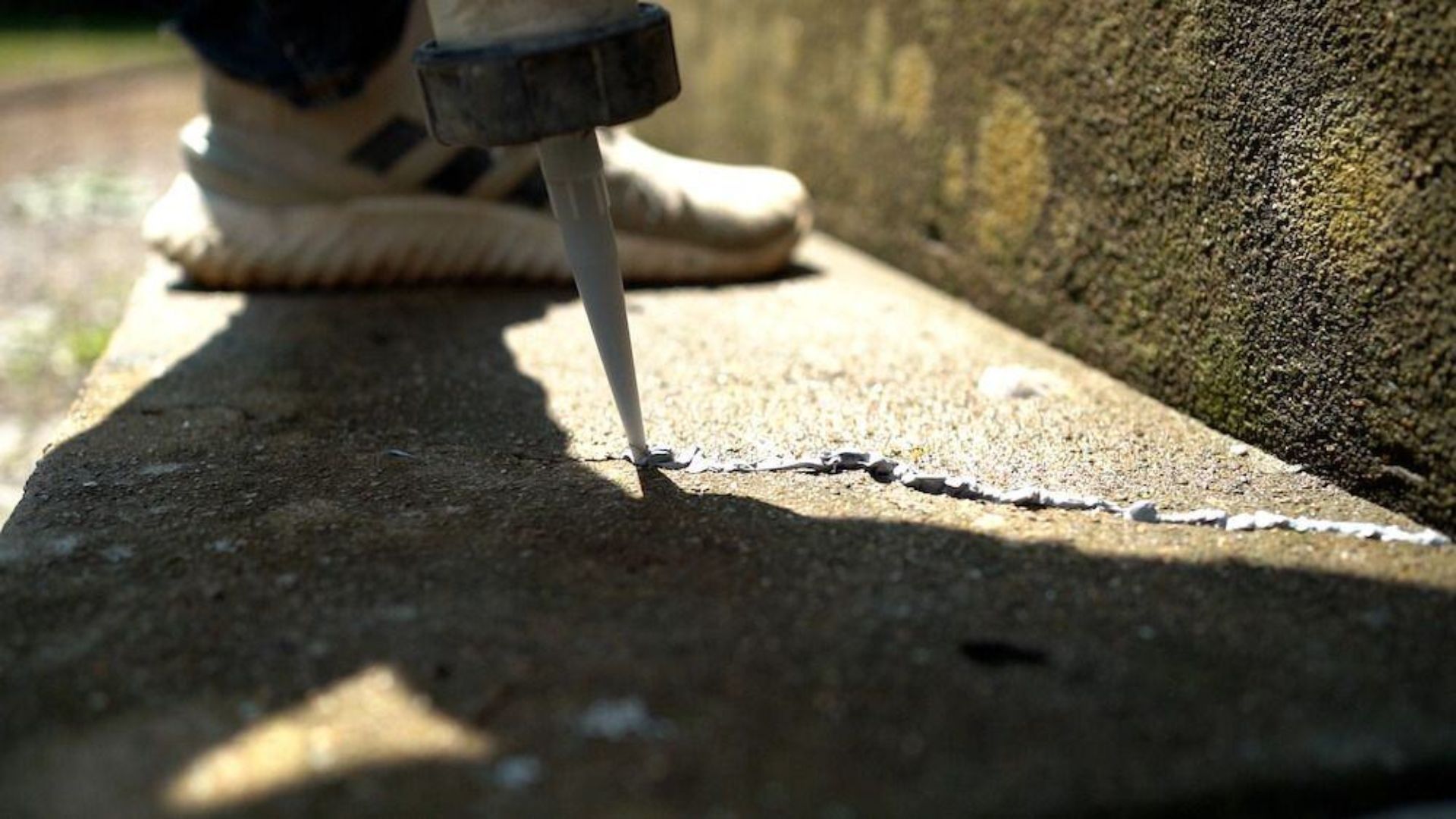
Preparing The Crack For Repair
Before you begin any concrete crack repair, it’s essential to properly prepare the area to ensure the repair lasts and adheres well. Skipping or rushing through these steps can lead to weak repairs that may not hold up over time. Follow these steps carefully for a smooth and lasting repair.
Step 1: Clean the Area
The first step in preparing a crack for repair is thoroughly cleaning the area. Over time, dirt, debris, and even loose concrete can accumulate in the crack, which can prevent the repair material from bonding properly. Here’s how to clean the area effectively:
- Start by sweeping the surface to remove loose dirt or debris from the crack and the surrounding area. A broom or a small hand brush can be used for this purpose.
- Use a wire brush to scrub the inside of the crack. This helps remove any smaller, stubborn particles of debris that may be clinging to the surface.
- Blow out or vacuum the crack after brushing to make sure no small particles or dust remain. A shop vacuum works well for this, but even using a can of compressed air can help to remove debris from deeper within the crack.
- For larger cracks, a pressure washer may be helpful to remove dirt or previous filler material. Just ensure the crack is completely dry before moving to the next step.
A clean crack allows the repair material to adhere directly to the concrete, ensuring a stronger and more durable repair.
Step 2: Widen the Crack
To ensure the new repair material bonds properly, you need to create a slightly larger surface area within the crack. This may sound counterintuitive, but widening the crack slightly will give the repair compound more surface to grip, leading to a stronger bond. Here’s how to do it:
- Use a cold chisel and hammer to carefully widen the crack. Hold the chisel at a slight angle to the crack, and gently tap it with the hammer to widen the opening. You don’t need to go too deep just enough to create a rough, uneven edge that will allow the repair material to grip onto the concrete better.
- Focus on creating an inward-sloping “V” shape, where the bottom of the crack is slightly narrower than the top. This shape helps the repair compound settle in and bond firmly as it cures.
- Remove any remaining debris from the widening process using your wire brush, vacuum, or compressed air again. The crack must be free of dust and particles before you proceed to the next step.
Widening the crack ensures that your repair material has enough surface to bond with, making the repair more effective and long-lasting.
Step 3: Remove Any Moisture
Moisture is a common enemy when it comes to concrete repair. If the crack is wet, the repair material won’t adhere properly, leading to weak spots or even further cracking down the road. Here’s how to make sure the crack is dry and ready for repair:
- Check for visible water or moisture inside the crack. If you’ve recently cleaned the area with water or if there has been rain, let the crack dry completely. This might take several hours or even a day or two, depending on weather conditions and the size of the crack.
- Use a heat gun or a hairdryer to speed up the drying process. If time is a factor or if you’re working in humid conditions, gently heat the crack area with a hairdryer or heat gun to evaporate any remaining moisture.
- For larger or deeper cracks, moisture can sometimes accumulate below the surface. If this is the case, use a blow dryer, or fan, or even let the crack air dry for longer periods before proceeding.
Dryness is key for a strong repair bond. Ensuring the crack is completely free from moisture will help the repair compound bond effectively, resulting in a longer-lasting repair.
By following these steps to clean, widen, and dry the crack, you’ll set a solid foundation for a successful and durable concrete repair. Proper preparation can make the difference between a quick fix and a repair that stands the test of time.
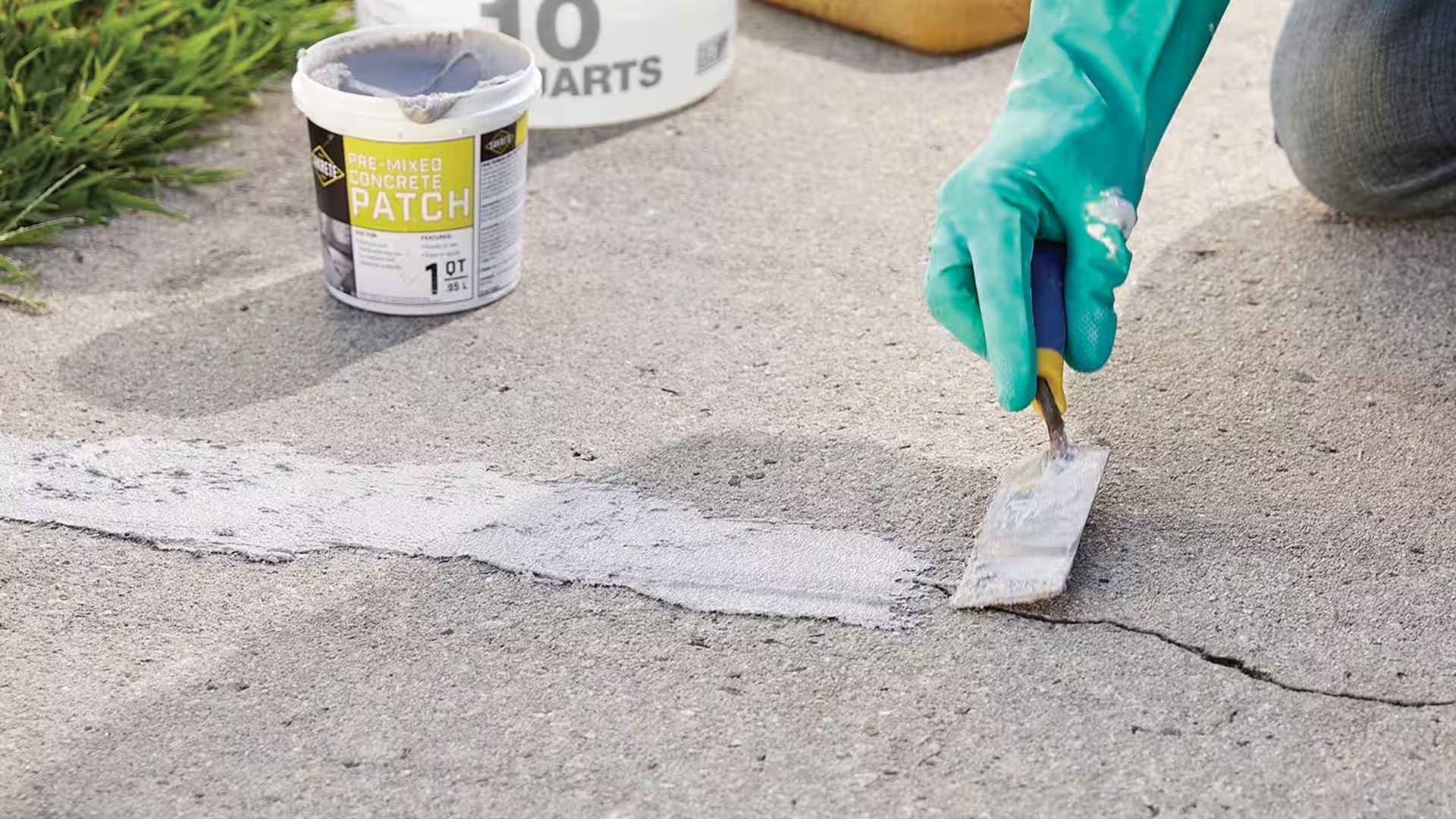
How To Repair Different Types Of Concrete Cracks
Concrete is a durable and reliable building material, but it’s not immune to cracks over time. Whether due to settling, shrinkage, or external forces, cracks can compromise the structural integrity of your concrete surface if left untreated. However, not all cracks are the same, and knowing how to repair each type properly is crucial for ensuring the longevity and strength of your concrete structures. Below, we’ll walk you through how to repair different types of concrete cracks, from small hairline fractures to more serious structural issues.
Repairing Small Hairline Cracks
Hairline cracks are shallow and narrow, typically less than 1/8 inch wide, and are often caused by concrete shrinkage or temperature changes. While they might seem insignificant, it’s important to address these cracks to prevent moisture penetration or further expansion.
Materials to Use
For repairing hairline cracks, using the right material is essential for long-lasting repair. The best options include:
- Liquid Crack Fillers: These are flexible fillers designed for fine cracks. They penetrate deeply into the crack and create a waterproof seal.
- Concrete Crack Sealers: This product can be applied to very small cracks and seal the surface, preventing future water infiltration and freeze-thaw damage.
Step-by-Step Process
1. Clean the Area: Before applying any product, thoroughly clean the crack. Use a stiff brush to remove any loose debris, dust, or dirt. For more stubborn grime, a wire brush or air compressor can be useful.
2. Apply the Filler or Sealer: After ensuring the crack is dry, use a liquid filler or crack sealer. These products often come in a bottle with a narrow nozzle for easy application. Pour the product directly into the crack, filling it to the surface.
3. Smooth the Surface: After applying the filler, use a putty knife or trowel to smooth the surface. This ensures a seamless finish and helps prevent water from pooling in the area.
4. Allow to Dry: Allow the material to cure as per the manufacturer’s instructions. In most cases, this takes 24 to 48 hours, but it’s important to keep the area dry and free from heavy traffic during this time.
Repairing Larger Cracks
Larger cracks, typically those wider than 1/8 inch, require more robust repair methods to restore the concrete’s integrity. These cracks may result from shifting foundations, heavy loads, or freeze-thaw cycles, and they can allow water to seep deeper into the concrete, causing further damage.
Materials to Use
- Concrete Patch Compound: For non-structural cracks, a concrete patch compound is a reliable choice. These compounds bond well to existing concrete and create a durable, weather-resistant repair.
- Hydraulic Cement: Ideal for situations where water seepage is present, hydraulic cement expands as it cures, providing a strong seal that resists water intrusion.
Step-by-Step Process
1. Clean and Prepare the Crack: Use a wire brush or grinder to widen the crack slightly and remove any loose material. This helps the patch compound adhere better.
2. Apply a Bonding Agent: For best results, apply a bonding adhesive to the inside of the crack. This ensures the patch material will adhere properly and prevents future separation. Most bonding agents can be brushed directly onto the surface.
3. Mix the Patch Material: Follow the instructions for mixing your concrete patch compound or hydraulic cement. These materials typically need to be mixed with water until they reach a putty-like consistency.
4. Fill the Crack: Using a trowel, press the patch material firmly into the crack, ensuring it fills the entire void. Smooth the surface with your trowel, blending it with the surrounding concrete.
5. Allow to Cure: The curing process is critical to the success of the repair. Make sure to follow the product’s recommended drying time and keep the area moist for several days to ensure a strong bond.
Using Epoxy for Structural Cracks
Structural cracks are the most serious type of crack, often indicating a compromise in the concrete’s integrity. These cracks can affect the stability of walls, foundations, or other load-bearing elements. Epoxy is one of the best solutions for repairing structural cracks because of its superior bonding strength and durability.
When to Use Epoxy
Epoxy is designed for deep, structural cracks, particularly when the crack compromises the overall strength of the concrete. This repair method is especially useful in foundations, walls, and large slabs, where a simple patch won’t be enough. Epoxy injections fill and seal the crack, restoring the concrete’s original strength and preventing further movement.
Step-by-Step Process
1. Prepare the Crack: Begin by cleaning the crack thoroughly. Use a wire brush or vacuum to remove all dust, debris, and loose material from within the crack.
2. Set Injection Ports: For deep structural cracks, install injection ports along the crack. These ports allow the epoxy to penetrate deep into the concrete. Place the ports every few inches along the length of the crack and secure them with epoxy paste.
3. Seal the Crack: Once the injection ports are in place, use the same epoxy paste to seal the surface of the crack between the ports. This ensures that when the epoxy is injected, it will not leak out of the surface.
4. Inject the Epoxy: Using an epoxy injection gun, begin injecting epoxy into the lowest port first. Gradually move up to the next port once the epoxy begins flowing out of the previous one. This method ensures the epoxy fills the crack.
5. Allow the Epoxy to Cure: After injecting the epoxy, let it cure according to the manufacturer’s instructions. Most epoxies will be cured within 24 hours, though curing times may vary depending on the product.
6. Remove the Ports and Finish: Once the epoxy has fully cured, remove the injection ports and any excess epoxy from the surface. If desired, you can grind the surface smooth to match the surrounding concrete.
Repairing concrete cracks is an essential maintenance task that can extend the life of your concrete structures and prevent more costly repairs in the future. By understanding the differences between hairline, larger, and structural cracks, and choosing the right materials and methods for repair, you can ensure a long-lasting, professional finish. Whether you’re a DIY enthusiast or seeking to enhance your knowledge for professional applications, following these detailed steps will help you successfully tackle any concrete crack repair project.
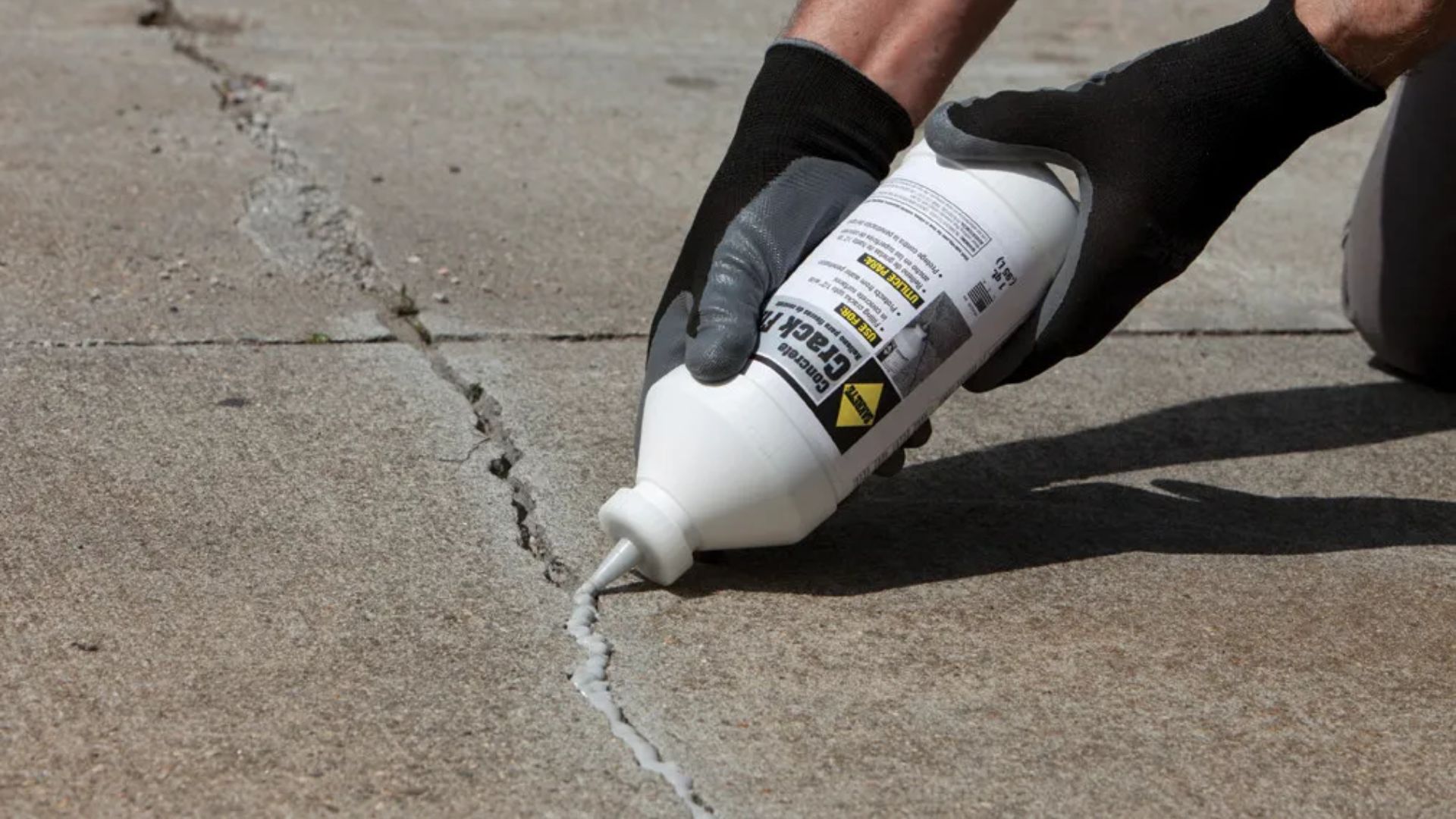
Curing And Finishing The Repair
When it comes to concrete repairs, the curing and finishing stages are crucial for ensuring a long-lasting, high-quality result. Here’s a breakdown of why proper curing matters, the different methods you can use, and how to finish the surface to match the surrounding area.
The Importance of Proper Curing
Curing is one of the most essential steps in concrete repair, as it directly impacts the durability and strength of the repair. When concrete dries too quickly, it can lead to cracks, surface imperfections, or weakened integrity. Proper curing allows the concrete to retain moisture during the initial drying period, ensuring it reaches its maximum strength and durability. Without adequate curing, even the best concrete repairs can fail prematurely, leading to further damage and costly repairs in the future.
Proper curing also enhances the concrete’s resistance to environmental factors such as freeze-thaw cycles, UV exposure, and chemical damage. By maintaining the right moisture levels, the repair will have a longer lifespan, protecting your investment for years to come.
Effective Curing Methods
There are several methods available for curing concrete, depending on the specific project and environmental conditions. Here are some widely used techniques:
- Plastic Sheeting: One of the simplest and most effective ways to cure concrete is by covering the repaired area with plastic sheeting. This method traps moisture and prevents the concrete from drying out too quickly. Be sure to tape or weigh down the edges of the plastic to keep it securely in place and prevent air from getting underneath.
- Curing Compounds: Curing compounds are chemical solutions that form a protective layer over the concrete. They work by sealing in moisture, allowing the repair to cure properly without excessive drying. These compounds are easy to apply with a sprayer or roller and are especially useful in larger repairs or areas with fluctuating weather conditions.
- Water Spraying: In some cases, keeping the concrete surface damp by regularly spraying it with water is an effective way to ensure proper curing. This method works well in warm or dry climates where moisture tends to evaporate quickly. However, you’ll need to monitor the area closely to ensure it remains consistently wet.
- Damp Burlap or Mats: Another method is placing damp burlap or similar moisture-retaining mats over the repair. This technique helps to lock in moisture while also allowing the concrete to breathe. Just make sure to keep the burlap wet throughout the curing process.
Each of these curing methods helps maintain the optimal moisture level within the concrete, which is essential for a strong, long-lasting repair.
Finishing the Surface for a Professional Look
Once the curing process is complete, it’s time to focus on finishing the surface to ensure it blends seamlessly with the surrounding concrete. A well-finished surface not only looks better but also helps prevent future damage by reducing the chances of moisture penetration or other environmental wear.
Here are some key tips for achieving a professional finish:
- Feathering the Edges: When repairing concrete, it’s important to feather the edges of the patch. Feathering involves smoothing the edges of the repair to create a gradual transition between the new and existing concrete. This helps the repair blend in more naturally and prevents a noticeable edge or ridge that could collect debris or water. Use a trowel to carefully taper the edges as you apply the repair material.
- Smoothing the Surface: To achieve a smooth finish, run a trowel over the surface while the concrete is still workable. If you’re aiming for a polished look, continue smoothing the surface in a circular motion with the trowel until it achieves the desired texture. For larger areas, you may need to use a float to help level the surface.
- Matching the Existing Texture: If the surrounding concrete has a specific texture such as a brushed or stamped finish it’s important to replicate that texture in your repair for a consistent look. For a brushed finish, lightly drag a stiff broom across the surface before it sets. For stamped patterns, use matching stamping tools while the concrete is still pliable. Taking the time to match the existing texture will ensure the repair is less noticeable and more cohesive.
By following these steps, you’ll ensure that your concrete repair is not only durable but also visually appealing. Proper curing and a well-finished surface can make a significant difference in the longevity of the repair and the overall appearance of your project.
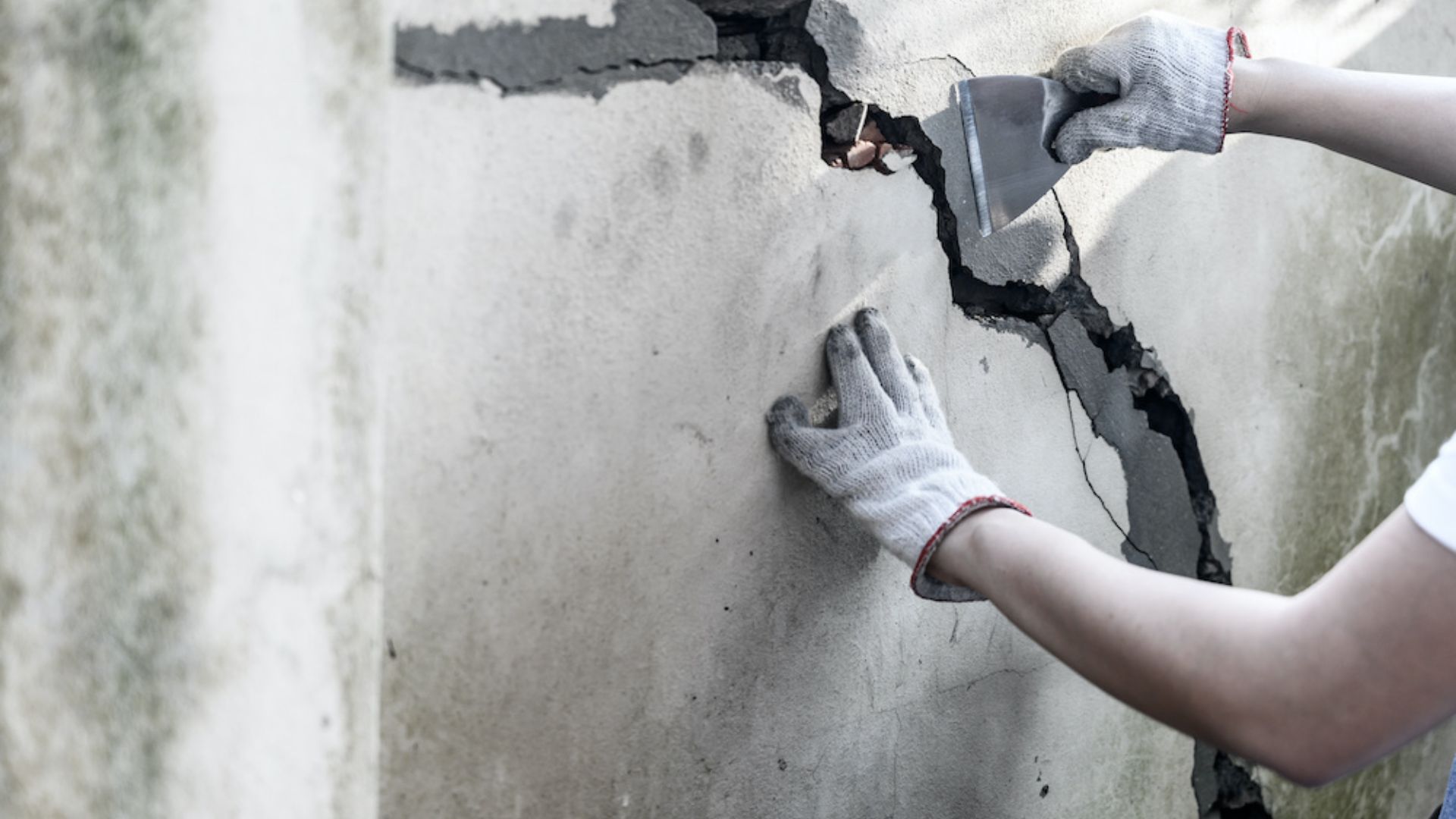
Preventing Future Cracks
When it comes to maintaining the longevity of concrete surfaces, taking proactive steps can make all the difference. Cracks are not just unsightly but can also weaken the structural integrity of the concrete over time. To prevent future cracks and keep your concrete in top shape, it’s crucial to focus on sealing, regular maintenance, and addressing drainage issues. Here’s a detailed look at how each of these practices can help.
Sealing the Surface
One of the most effective ways to protect your concrete surface from potential damage is by applying a high-quality concrete sealer. Concrete is naturally porous, which means that water can easily seep into the surface. Over time, this water can cause the concrete to expand and contract with changing temperatures, leading to cracks. Sealing the surface creates a protective barrier that prevents water, oil, and other harmful substances from penetrating the concrete.
A good concrete sealer not only helps with water resistance but also adds an extra layer of protection against UV damage and wear from daily use. This is particularly important for driveways, patios, or any outdoor concrete surfaces exposed to the elements. Applying a sealer is a relatively simple task that can be done every few years to ensure the surface stays in optimal condition.
Regular Maintenance
Routine maintenance plays a vital role in preventing cracks and extending the life of your concrete. Regularly inspecting your concrete for early signs of wear or damage allows you to catch potential issues before they become major problems. Look out for small cracks, chips, or uneven surfaces, as these can be indicators of underlying damage.
Cleaning your concrete surfaces regularly is another important maintenance step. Dirt, debris, and chemicals from things like oil spills or de-icing salts can accelerate the deterioration of concrete. By keeping the surface clean, you reduce the risk of these substances breaking down the concrete over time. Use a pressure washer or a concrete-specific cleaner to keep your surfaces looking their best.
Addressing Drainage Issues
Water is one of the biggest culprits when it comes to concrete damage, so ensuring proper drainage around your concrete surfaces is crucial. Poor drainage allows water to pool on or around your concrete, which can lead to cracks as the water seeps in and freezes during colder months. Additionally, standing water can erode the soil beneath the concrete, leading to sinking or uneven surfaces over time.
To prevent these issues, check that your property has proper drainage solutions in place. Gutters, downspouts, and grading should be designed to direct water away from concrete surfaces. If needed, consider installing a French drain or improving landscaping to help channel water effectively. Ensuring that water flows away from your concrete will greatly reduce the risk of cracks forming due to water-related damage.
In conclusion, preventing future cracks in your concrete involves a combination of protective measures and ongoing care. By sealing the surface, committing to regular maintenance, and addressing drainage issues, you can significantly extend the life of your concrete surfaces, keeping them looking great and functioning well for years to come.
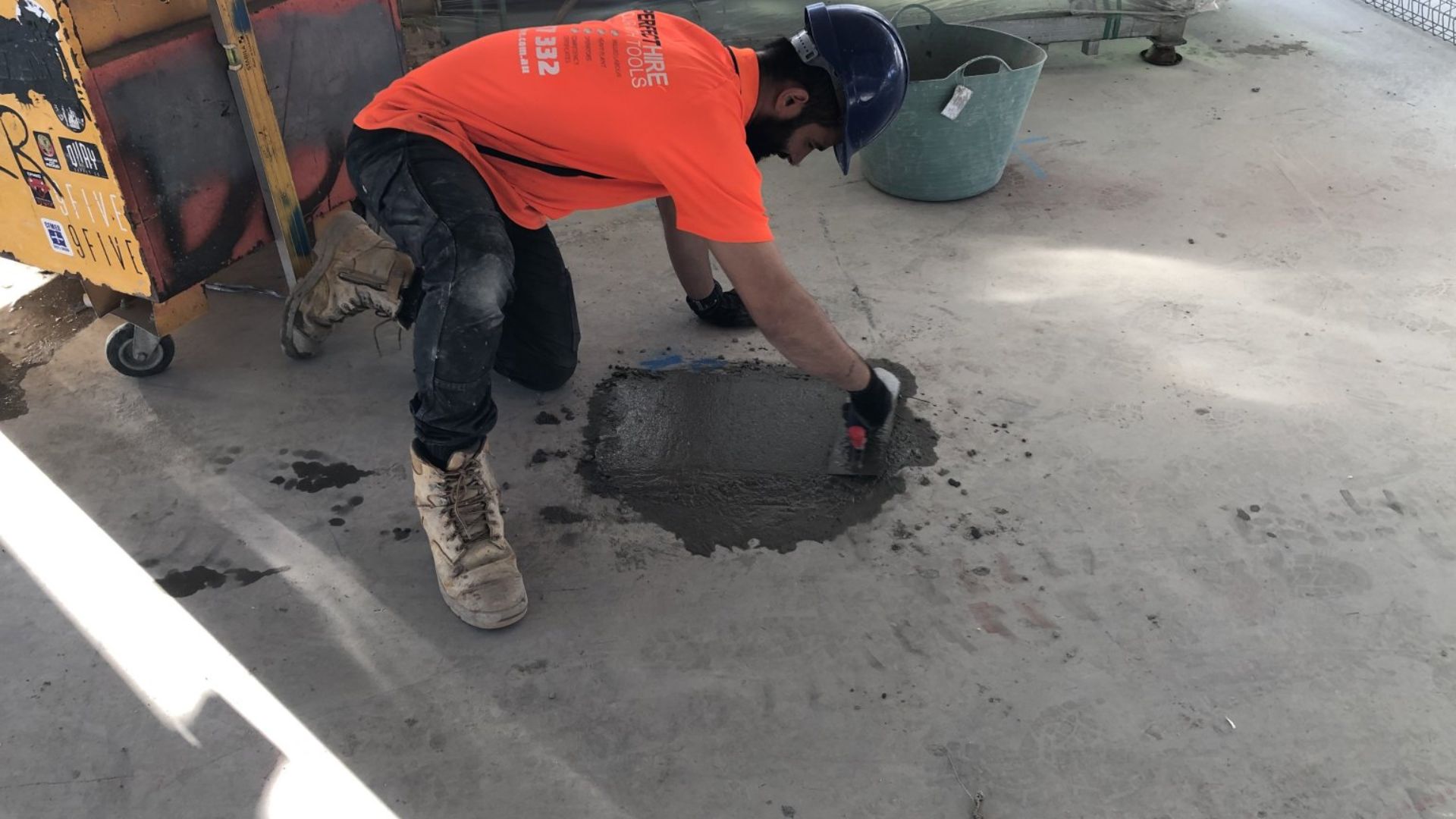
When To Call A Professional
Knowing when to handle concrete repairs yourself and when to call a professional is crucial for maintaining the longevity and safety of your concrete surfaces. While minor cracks or surface-level wear can sometimes be addressed with DIY methods, certain signs of damage require the expertise of a professional to ensure the problem is thoroughly and correctly repaired. Here’s what to look out for and what to expect when calling in the experts.
Signs of Serious Concrete Damage
Not all cracks or imperfections in your concrete are equal. Some may be superficial and purely cosmetic, but others are indications of more significant structural issues that should be addressed by a professional. Here are some key signs that it’s time to bring in a professional concrete contractor:
- Deep Cracks: If the cracks in your concrete are more than just surface-level and penetrate deeper into the material, this could be a sign of structural weakness. These deep cracks can allow moisture to seep in, potentially causing further damage over time, including freeze-thaw cycles that exacerbate the problem.
- Sinking or Shifting Slabs: Uneven or sinking concrete slabs often point to issues with the foundation or soil beneath the surface. This could be caused by soil erosion, improper settling, or poor installation techniques. A professional can assess the root cause of the problem and suggest the best repair method, which might involve lifting or leveling the concrete.
- Recurrent Cracking: If you’ve repaired cracks before and they keep reappearing, it’s a sign that the underlying issue hasn’t been properly addressed. Recurrent cracks can indicate problems with the foundation or the load-bearing capacity of the concrete. A professional can identify why these cracks keep returning and provide a long-lasting solution.
- Severe Surface Deterioration: Over time, concrete can wear down due to exposure to harsh weather conditions, heavy loads, or chemical spills. If the surface is crumbling, spalling, or flaking, this type of damage may be beyond simple DIY fixes and could require professional resurfacing or replacement.
Costs and Considerations for Professional Concrete Repairs in NZ
When considering professional concrete repair services in New Zealand, the cost will vary depending on the extent of the damage and the complexity of the repair required. Here are a few factors to keep in mind:
- Size and Scope of the Repair: Minor repairs like filling small cracks or applying a sealant can be relatively inexpensive, whereas more significant jobs, such as lifting and leveling sunken slabs or replacing entire sections of concrete, will naturally cost more.
- Type of Repair Method: Different issues may require different approaches. For example, slab jacking or foam injection techniques to raise sunken concrete tend to cost more than simple patching methods. Resurfacing an entire driveway or patio will also be more expensive than addressing localized cracks.
- Labor and Materials: Labour costs in New Zealand will also factor into the overall expense. Higher-end materials, like polymer-based sealants or specialized coatings, may increase the cost, but they can also offer better durability and protection over time.
To give a rough idea, basic concrete repairs in NZ may start from around $200 to $500 for small jobs, but more extensive repairs or resurfacing could range from $1,000 to $5,000 or more. It’s always wise to get multiple quotes from reputable contractors to ensure you’re getting the best value for your money.
In conclusion, recognizing when to call a professional can save you time, money, and the headache of dealing with recurring issues. Whether it’s deep cracks, shifting slabs, or persistent surface damage, professional concrete contractors in New Zealand can offer expert solutions to ensure your concrete surfaces remain safe and durable for years to come.
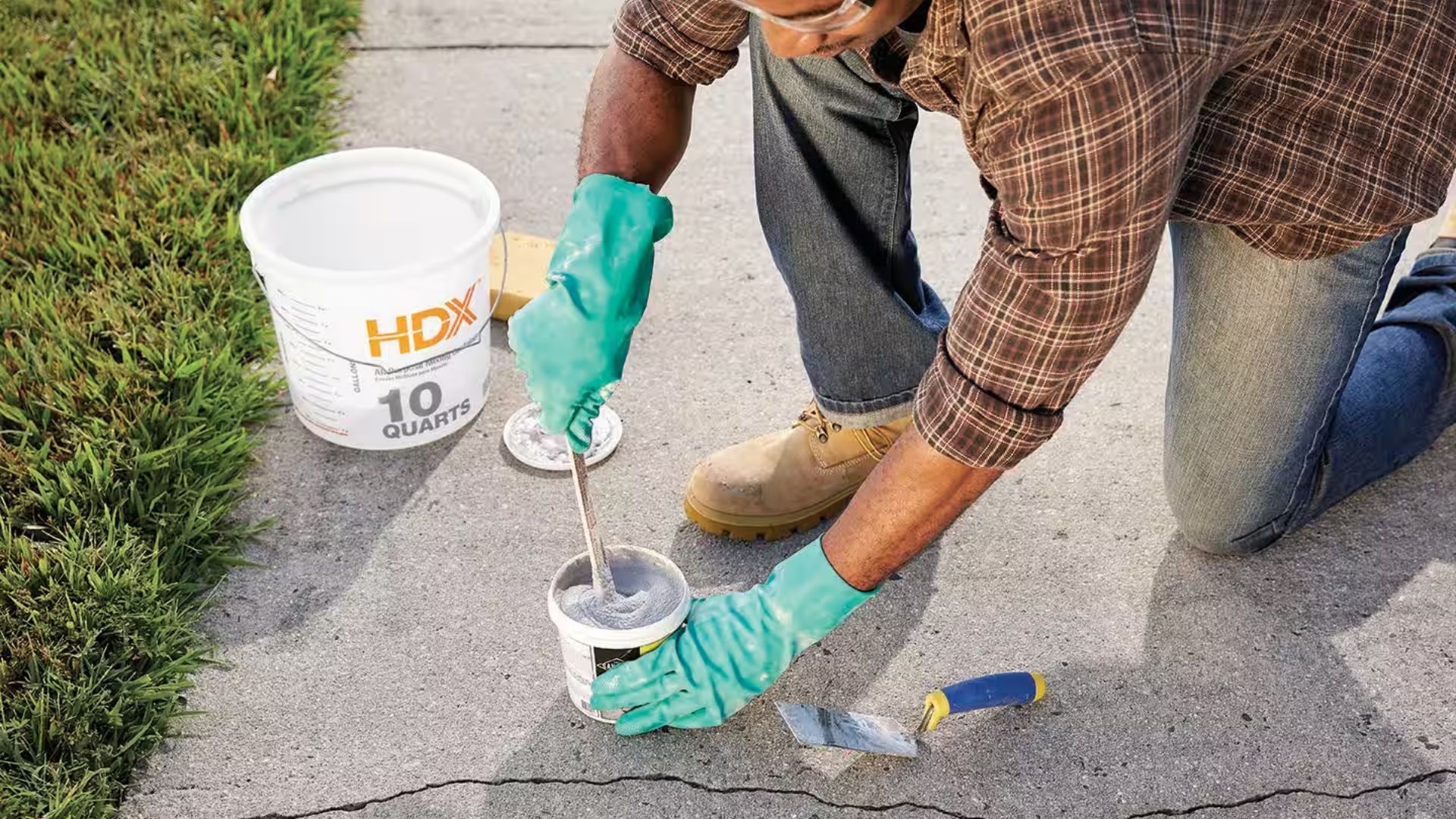
Eco-Friendly Concrete Repair Solutions
Concrete repair is an essential part of maintaining the longevity and structural integrity of your home, but it can also be done in an eco-friendly way. With the growing concern for the environment, homeowners are increasingly looking for sustainable solutions that minimize their carbon footprint. Here’s a look at some eco-friendly concrete repair options that not only help the planet but also provide long-lasting results for your home.
Sustainable Materials for Concrete Repair
When it comes to eco-friendly concrete repair, the choice of materials is crucial. Traditional concrete and sealants often rely on energy-intensive processes and non-renewable resources, but newer, greener alternatives are available. Here are some sustainable materials to consider:
- Green Concrete Repair Products: Green concrete refers to concrete made with less energy-intensive materials and processes. This type of concrete often uses supplementary cementitious materials (SCMs) like fly ash, slag cement, or silica fume, which reduce the overall environmental impact. These materials help lower CO2 emissions by replacing a portion of the cement, the most carbon-intensive component in traditional concrete.
- Sustainable Sealants: Eco-friendly sealants, made from natural and non-toxic ingredients, are another excellent choice for repairing cracks and joints in concrete surfaces. These sealants reduce harmful emissions both during production and after application. Many green sealants are made from renewable resources and are designed to last longer, meaning fewer repairs and less material waste over time.
Recycling and Reuse in Concrete Repairs
Reducing waste is a key component of eco-friendly concrete repair. One way homeowners can minimize waste is by incorporating recycled materials into their concrete repairs. Here are two important approaches:
- Incorporating Recycled Aggregates: Rather than using virgin aggregates (such as newly quarried sand and gravel), recycled aggregates can be sourced from crushed concrete or other construction waste. This approach reduces the demand for new resources and prevents waste from ending up in landfills. Additionally, recycled aggregates often perform just as well as new ones, making them a practical and sustainable option for concrete repairs.
- Reusing Existing Materials: In some cases, homeowners can reuse parts of the existing concrete structure, which not only saves money but also reduces waste. For example, when repairing a cracked concrete surface, you may be able to keep most of the original material intact and only replace the damaged sections. This reduces the amount of new concrete needed and helps to conserve resources.
Why Choose Eco-Friendly Concrete Repair?
Choosing eco-friendly concrete repair solutions offers several benefits beyond just helping the environment:
- Cost-Effectiveness: Many sustainable materials are designed to be more durable, which means fewer repairs over the lifespan of the concrete. This saves homeowners money in the long run.
- Healthier Living Environment: Using non-toxic and natural sealants and materials can improve indoor air quality, making your home healthier for you and your family.
- Reduced Carbon Footprint: By using recycled materials and reducing the need for new concrete, homeowners can significantly lower the carbon footprint associated with their repairs.
Incorporating sustainable practices into your concrete repairs is a simple yet impactful way to contribute to a greener future. With options like green concrete, eco-friendly sealants, and recycled aggregates, it’s easier than ever to maintain your home while minimizing your environmental impact.
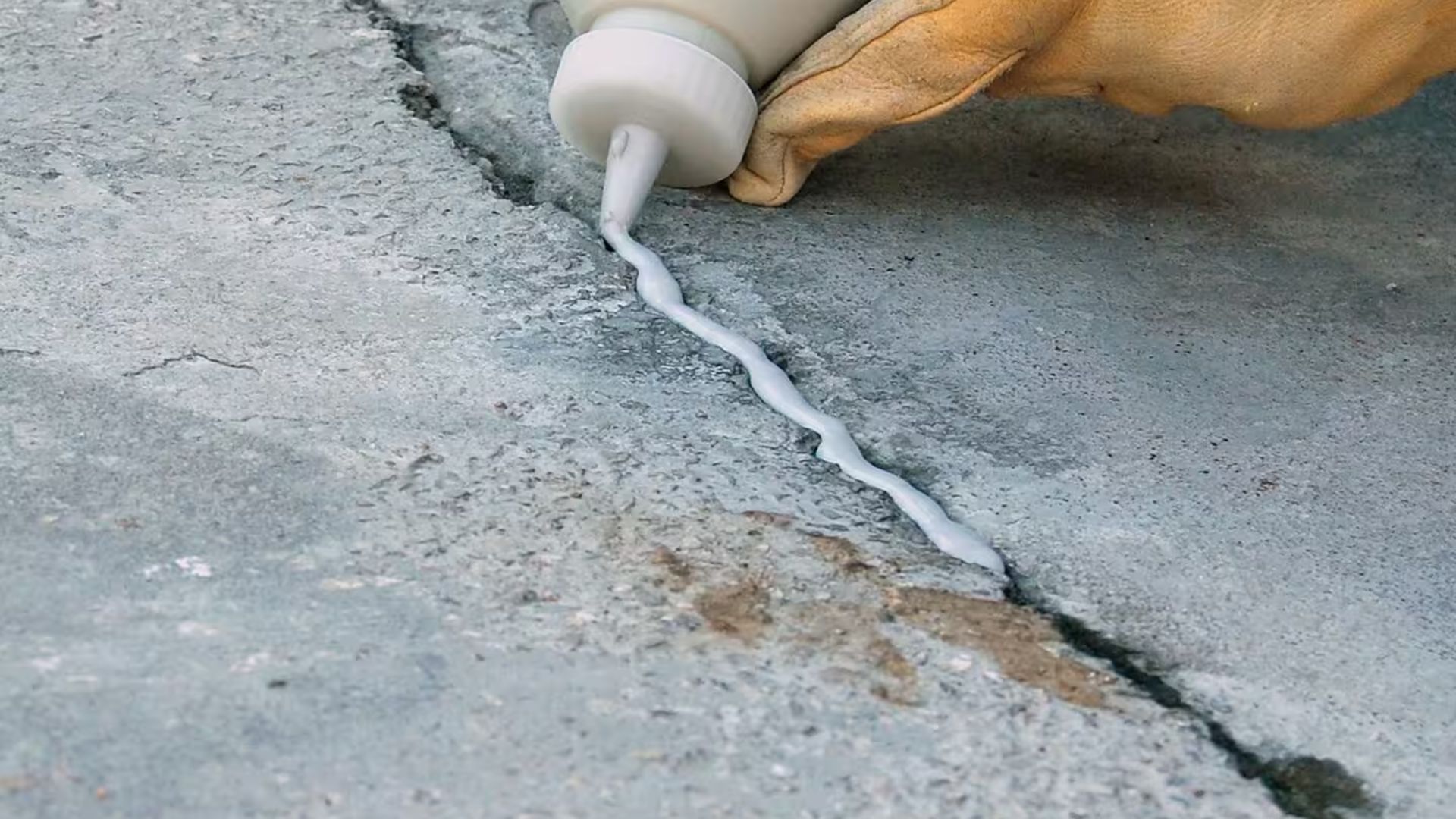
FAQs: About How To Repair Cracks In Concrete NZ
Conclusion
Addressing cracks in concrete promptly is essential to prevent further damage and costly repairs down the line. By following the right steps cleaning the crack, preparing the surface, applying the appropriate filler, and ensuring proper curing you can extend the lifespan of your concrete surfaces. Whether you choose to tackle minor repairs on your own or seek professional help for more significant issues, taking action now will protect your property in the long run. If you’re looking for more tips on concrete maintenance, consider subscribing to our newsletter or reaching out to local repair experts for personalized advice and solutions.
About the Author:
Mike Veail is a recognized digital marketing expert with over 6 years of experience in helping tradespeople and small businesses thrive online. A former quantity surveyor, Mike combines deep industry knowledge with hands-on expertise in SEO and Google Ads. His marketing strategies are tailored to the specific needs of the trades sector, helping businesses increase visibility and generate more leads through proven, ethical methods.
Mike has successfully partnered with numerous companies, establishing a track record of delivering measurable results. His work has been featured across various platforms that showcase his expertise in lead generation and online marketing for the trades sector.
Learn more about Mike's experience and services at https://theleadguy.online or follow him on social media: