Welcome to our comprehensive guide on understanding the concrete price per m3 in New Zealand. Whether you’re planning a small DIY project or a large-scale construction job, knowing the cost of concrete is crucial for budgeting and ensuring you’re getting the best value for your money. In this post, we’ll break down the average cost of concrete per cubic meter in NZ, explore the key factors that affect these prices, and provide practical tips to help you save on your next project. By the end, you’ll have all the information you need to make informed decisions about purchasing concrete and managing your project efficiently.
The average concrete price per m³ in New Zealand typically ranges from $180 to $220, depending on factors like location, concrete mix type, and additional services such as delivery or pumping. Prices can vary across regions and may increase for specialized mixes or decorative finishes. To get the best value, compare quotes from local suppliers and consider bulk ordering for larger projects.
- What Is The Average Concrete Price Per M³ In NZ?
- Factors That Affect the Cost Of Concrete In NZ
- Comparing Prices Across Different Concrete Suppliers In NZ
- How To Calculate The Total Concrete Cost For Your Project
- DIY Vs. Hiring A Contractor
- Tips For Getting The Best Value For Your Concrete Purchase
- FAQs: About Concrete Price Per M³ NZ
- Conclusion
What Is The Average Concrete Price Per M³ In NZ?
When you’re planning a construction project in New Zealand, one of the essential factors to consider is the cost of concrete. The price of concrete per cubic meter (m³) can vary depending on a range of factors, including location, supplier, and the type of concrete you need. Here’s an in-depth look at the current concrete pricing landscape in NZ to help you budget more accurately.
Current Price Range
In New Zealand, the average price for concrete per cubic meter generally falls between $180 and $220/m³. However, it’s important to understand that this range can shift depending on several factors, including your geographical location and the specific supplier you choose.
- Auckland tends to be at the higher end of the price range due to higher demand and transportation costs.
- Wellington and Christchurch typically offer prices within the mid-range.
- If you’re in rural areas, prices can be lower or higher depending on proximity to suppliers, transportation costs, and the availability of materials. It’s worth noting that if you’re in a more remote location, the price per cubic meter could increase due to the extra cost involved in delivering materials to your site.
Additionally, prices can fluctuate seasonally, often rising in the warmer months when construction projects are in full swing and demand for concrete increases.
Types of Concrete and Their Costs
Different types of concrete can also affect the overall cost per cubic meter. Here’s a breakdown of the common types and their relative costs.
- Standard concrete: This is the most commonly used type for general construction, like foundations and driveways. It falls within the typical price range of $180–$220/m³.
- High-strength concrete: Used for specialized projects that require greater durability, such as commercial buildings or bridges. This type of concrete can cost more, typically ranging from $200 to $250/m³, depending on the strength needed.
- Decorative concrete: If you’re looking to enhance the aesthetics of your project with stamped, colored, or exposed aggregate concrete, expect to pay a premium. Decorative concrete can range from $220 to $280/m³ or more, depending on the design complexity and the finishing process involved.
Why Prices Vary
Several factors contribute to the variation in concrete prices across New Zealand.
- Location: As mentioned earlier, where you’re based will have a significant impact on the cost. Urban areas often have more competitive pricing due to the concentration of suppliers, while rural or remote areas might see higher prices due to transportation costs.
- Local demand: In areas where there is a high demand for construction materials, such as during peak building seasons or in fast-growing cities like Auckland, prices tend to rise. Conversely, during off-peak times or in regions with lower construction activity, prices may stabilize or even decrease slightly.
- Transport costs: Concrete is a heavy material, and transportation can be a major contributor to the final cost. If the supplier is located far from your site, the delivery charges will be higher, pushing up the price per cubic meter.
- Supplier differences: Not all suppliers offer the same price, even in the same region. Some suppliers might charge more for premium-quality materials or quicker delivery times, while others may offer discounts for bulk orders. It’s always a good idea to compare quotes from multiple suppliers before making a decision.
While the typical price of concrete in New Zealand ranges from $180 to $220 per m³, several factors, including location, type of concrete, and market demand, can cause variations. Be sure to consider all these elements when budgeting for your next project to ensure you get the most accurate estimate.
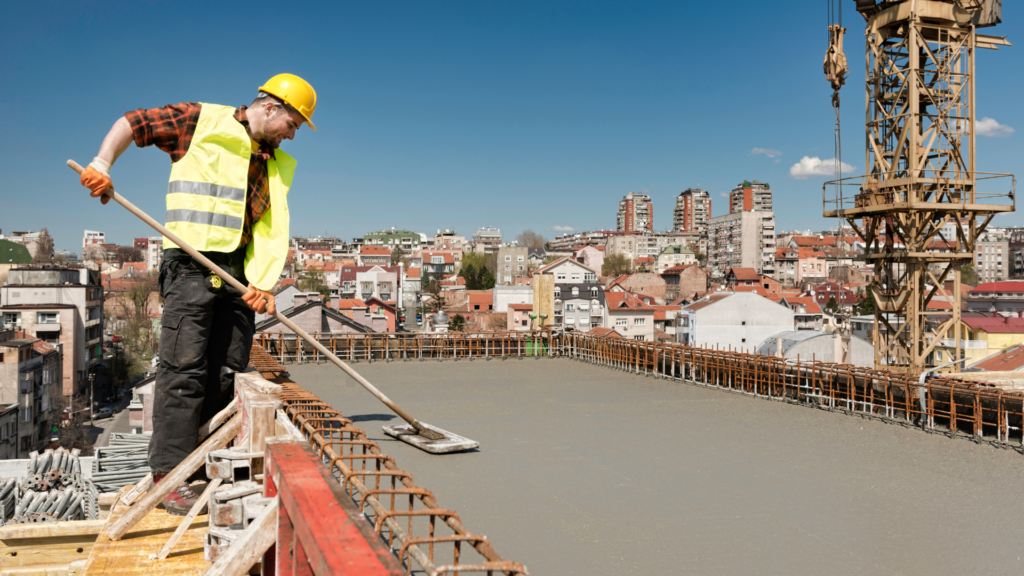
Factors That Affect the Cost Of Concrete In NZ
When planning a concrete project in New Zealand, it’s important to understand the various factors that can impact the overall cost. Concrete prices per cubic meter can fluctuate based on several variables, including the mix type, location, order size, and additional services. This section breaks down each of these factors to help you better estimate the total expense for your project.
Concrete Mix and Strength
One of the primary factors affecting the cost of concrete is the type of mix and the strength required. Concrete is typically classified by its strength, measured in megapascals (MPa). Common strength grades include 20MPa, 25MPa, and 30MPa, each designed for specific applications.
- 20MPa Concrete: This lower-strength mix is often used for projects like footpaths, patios, and residential driveways where the load is relatively light.
- 25MPa Concrete: Suitable for slightly heavier loads, this mix is commonly chosen for foundations or heavier residential driveways.
- 30MPa Concrete: This high-strength option is frequently used in commercial settings or for structural projects, such as large foundations and industrial floors.
In general, the higher the MPa, the more expensive the concrete will be per cubic meter. Projects that require higher strength, like commercial foundations or areas with heavy traffic, will typically cost more due to the increased quality of materials and additives required for durability.
Location and Delivery Fees
Where your project is located plays a significant role in the total cost of concrete. Proximity to the nearest concrete plant can influence delivery charges, with prices rising as the distance from the supplier increases. This is particularly true in more rural areas where concrete plants are sparse.
- Proximity to Concrete Plants: If your site is close to a concrete supplier, you’ll likely benefit from lower delivery fees. However, projects in remote or rural areas may face higher delivery costs due to the increased travel time for trucks.
- Traffic and Access Issues: The accessibility of your site can also affect delivery costs. If your site is located in a hilly area or is difficult to access, the supplier may charge extra for the complexity involved in reaching your project. Additionally, traffic congestion can increase delivery times, leading to further costs.
Quantity Ordered
The volume of concrete you order can directly influence the price per cubic meter. Larger orders often benefit from economies of scale, meaning the cost per cubic meter decreases as the volume increases.
- Bulk Orders vs. Small Orders: When ordering a large quantity of concrete for a major project, such as laying the foundation for a building, the price per cubic meter is often lower than for smaller projects like a backyard patio.
- Minimum Order Requirements: Many suppliers have a minimum order quantity, which is the smallest volume of concrete they will deliver. If your project is small and doesn’t meet the minimum, you may incur additional charges or need to pay for more concrete than you need.
Additional Costs: Pumping, Pouring, and Finishing
The complexity of your project can significantly add to the total cost. While basic concrete pouring may be included in the price, more complicated jobs often require additional services.
- Pumping: If the concrete needs to be pumped to hard-to-reach locations, such as elevated areas or sites far from the road, the cost of hiring a concrete pump will be added to your bill. Pumping services can vary widely in price, depending on the complexity of the job.
- Finishing: Some projects require more than just basic concrete. If you opt for decorative finishes like exposed aggregate, colored concrete, or stamped designs, expect to pay extra. These finishes can enhance the aesthetic appeal of driveways, patios, and outdoor areas, but they will increase your overall expenses.
Seasonality and Demand
The time of year you plan your concrete project can also influence the price. In New Zealand, concrete demand tends to fluctuate with the seasons and construction industry trends.
- High-Demand Seasons: During the summer months or peak construction seasons, concrete prices may rise due to increased demand. Contractors and suppliers are busier, and this can push up prices due to limited availability of materials and labor.
- Off-Peak Periods: In contrast, prices may be slightly lower during off-peak periods, such as winter, when construction activity slows down. Taking advantage of these times could result in cost savings for your project.
Several factors influence the cost of concrete in New Zealand, including the type and strength of the mix, location and delivery fees, the quantity ordered, additional services like pumping and finishing, and even seasonal demand. By understanding how these elements affect pricing, you can better plan and budget for your project, ensuring you get the best value for your money. Whether you’re laying a driveway or pouring the foundation for a new home, these insights will help you navigate the variables that impact the final cost of concrete.
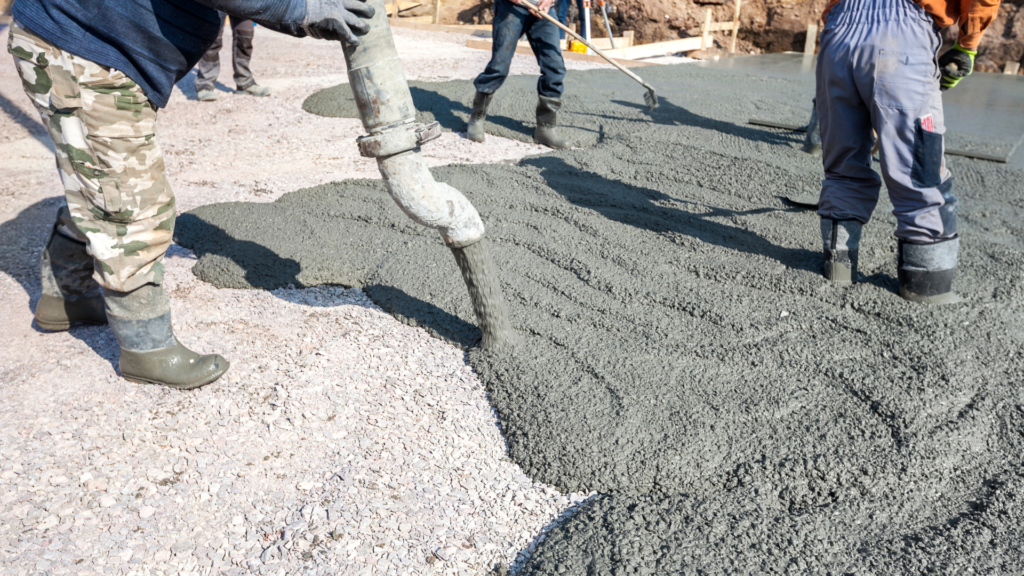
Comparing Prices Across Different Concrete Suppliers In NZ
When undertaking any construction project in New Zealand, whether it’s a driveway, foundation, or a large commercial venture, choosing the right concrete supplier is crucial. Prices and services can vary widely depending on the supplier, so understanding how to compare options and make an informed decision is essential for ensuring the best results for your project. Below, we’ll break down how to find reliable suppliers, compare prices between local and national brands, and how to analyze the quotes you receive to make sure you’re getting the best deal.
How to Choose a Reliable Supplier
Finding a reliable concrete supplier is about more than just price it’s about quality, service, and reputation. Here’s a step-by-step guide to help you choose a trustworthy supplier.
- Look for Reviews and Testimonials: The first step in finding a reliable concrete supplier is to do some research. Check online reviews on platforms like Google or TradeMe, where past customers often share their experiences. Local forums and Facebook groups for builders and DIYers can also provide firsthand insights into the reliability of local suppliers. Pay attention to comments about punctuality, product quality, and customer service.
- Ask for Quotes from Multiple Suppliers: Once you’ve shortlisted potential suppliers, reach out to them for quotes. Asking for multiple quotes allows you to compare not only the price but also the services included in the offer. Some suppliers might include delivery or pumping services at no extra cost, while others might charge separately. More on this below.
- Assess Customer Service: The way a supplier handles your initial inquiry says a lot about their customer service. Are they responsive and willing to answer questions? Do they provide clear and detailed information? Communication is key, especially if issues arise during the project.
- Utilize Online Resources and Local Directories: Local directories such as Yellow Pages, Neighbourly, or NZ Concrete Society can be excellent resources to find reputable suppliers. Additionally, websites like Builderscrack or Houzz may feature highly rated concrete suppliers in your area.
- Ask for Builder Recommendations: Builders often have firsthand experience working with different suppliers. If you’re working with a contractor, ask for their recommendations—they may even have preferred suppliers who offer them discounts or better service due to long-term relationships.
Local Suppliers vs. Nationwide Brands
When comparing prices for concrete, you’ll notice that local suppliers and nationwide brands offer different benefits. Here’s a look at the pros and cons of each.
- Local Suppliers:
- Pros: Local suppliers often offer personalized service and may have more flexibility in delivery times, especially in rural areas. They can also be more invested in the community, which can result in better customer service. You might even find that local suppliers offer better prices for smaller projects due to reduced transportation costs.
- Cons: Smaller suppliers may not have the capacity to handle larger projects or offer the same discounts that bigger, national brands can for bulk orders.
- Nationwide Brands:
- Pros: Well-known brands have the capacity to handle large-scale projects and can often offer bulk discounts. Their larger fleet of trucks and resources means you’re likely to have more reliable delivery options. They also often have established systems and processes that smaller suppliers may lack.
- Cons: These larger brands might charge higher prices due to their overhead costs. Also, in some cases, their customer service can feel more impersonal, as you may not be dealing with the same representative throughout your project.
Whichever option you choose, always factor in the delivery distance. Sometimes a local supplier might end up being more cost-effective once delivery fees are accounted for, even if their base price per cubic meter of concrete is slightly higher.
Requesting and Analyzing Quotes
When requesting quotes from concrete suppliers, it’s important to provide detailed information to ensure the quotes you receive are accurate and comparable. Here’s how to approach this.
- What Information to Provide: When reaching out to suppliers for a quote, include the size of the project (in cubic meters) and the type of concrete you need (e.g., standard, high-strength, or specialty mixes). Let them know if there are any specific delivery requirements, such as tight access or if you need additional services like pumping.
- What to Look for in a Quote: The devil is in the details, so when you receive quotes, carefully review the breakdown of costs. Here are some key things to look for:
- Delivery Fees: Are delivery costs included in the quote? Some suppliers charge extra for delivery based on distance or time, so make sure this is factored in.
- Pumping Services: If your site requires the concrete to be pumped, ask if this service is included in the quote or if it comes at an additional charge.
- Extra Costs: Be on the lookout for hidden fees or costs not itemized in the quote. Ask if they charge extra for weekend delivery, out-of-hours service, or handling concrete additives like fibers or color.
- Discounts for Bulk Orders: If your project is large, ask if the supplier offers discounts for bulk orders. This is often the case with nationwide suppliers, but some local companies may offer this as well, particularly if you negotiate.
- Comparing the Quotes: Once you have multiple quotes, compare them not only on price but also on what’s included. Sometimes a quote that appears cheaper at first glance might end up costing more due to added services that other suppliers include in their price. Don’t hesitate to ask for clarification if something is unclear in a quote.
By following these steps, you’ll be better equipped to compare prices from various concrete suppliers in New Zealand and make an informed decision that balances cost, quality, and service. In doing so, you can ensure the success of your construction project while sticking to your budget. Choosing the right concrete supplier in New Zealand doesn’t have to be complicated, but it does require a bit of research and comparison. By considering factors like reputation, customer service, and pricing breakdowns, you can confidently select a supplier that meets your needs and helps your project run smoothly from start to finish.
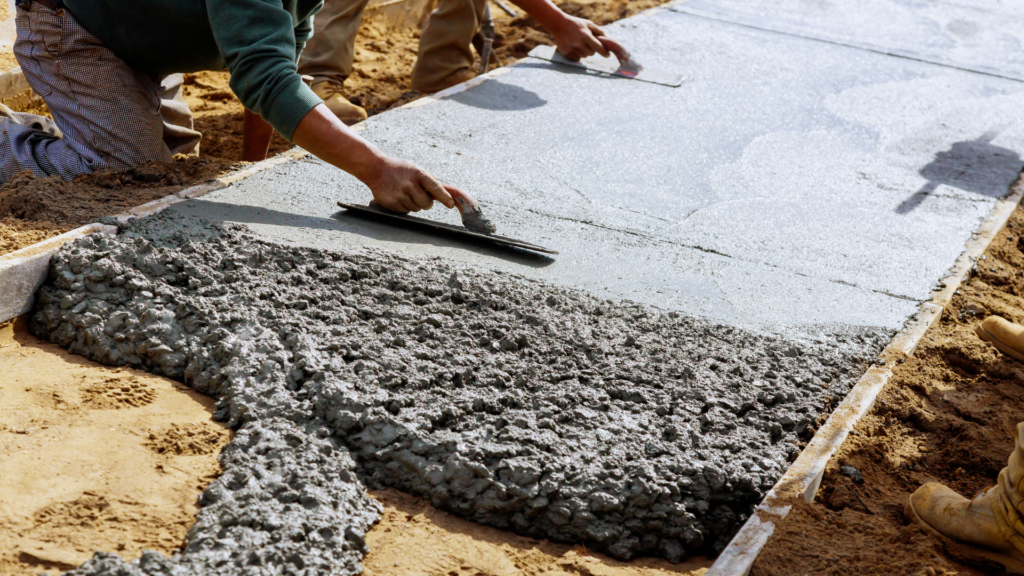
How To Calculate The Total Concrete Cost For Your Project
Accurately estimating the total cost of concrete for your project is essential for staying within budget and avoiding surprises. Whether you’re working on a driveway, patio, or foundation, calculating costs properly helps you prepare for both material and labor expenses. In this guide, we’ll walk you through the process step by step.
Estimate the Volume of Concrete Needed
The first and most important step is calculating how much concrete your project will require. This involves measuring the dimensions of the space and using a simple formula to estimate the volume.
To find the volume of concrete needed, multiply the length, width, and depth of the area. For example, if you are pouring a driveway that is 10 meters long, 4 meters wide, and 0.15 meters thick, you would multiply these dimensions.
- Length = 10 meters
- Width = 4 meters
- Depth = 0.15 meters
So, the volume of concrete required is 10 x 4 x 0.15 = 6 cubic meters.
Tips for Choosing the Correct Thickness
The thickness of concrete will vary depending on the type of project you’re working on. Here are some guidelines to help you determine the correct thickness.
- Driveways: Typically require a thickness of 100mm to 150mm (4 to 6 inches) to support the weight of vehicles.
- Patios: Can usually be thinner, around 75mm to 100mm (3 to 4 inches), since they only bear foot traffic and light furniture.
- Foundations: Will depend on the type of structure being built, but a common residential foundation slab is between 150mm and 200mm (6 to 8 inches) thick.
Accurate measurement is key to ensuring you purchase the correct amount of concrete, which will help you avoid overspending or coming up short.
Calculate the Total Concrete Cost
Once you’ve estimated the volume of concrete needed, the next step is to calculate the cost. The price of concrete is typically calculated per cubic meter. To find your total cost, multiply the volume of concrete by the price per cubic meter.
For instance, if the price of concrete is $120 per cubic meter and your project requires 6 cubic meters, the total cost would be 6 x $120 = $720.
Accounting for Wastage
To avoid running short or facing delays, it’s a good idea to add an additional 5-10% to your volume calculation. This extra allowance will cover any spills, uneven terrain, or minor miscalculations. For example, if your original estimate was 6 cubic meters, adding 10% would mean ordering 6.6 cubic meters of concrete. This adjustment brings your total cost to 6.6 x $120 = $792.
Factor in Additional Expenses
Concrete costs aren’t just limited to the material itself. There are additional expenses you need to account for, depending on the complexity and scale of your project.Common Additional Costs Include.
- Delivery Charges: Most concrete suppliers charge a fee for delivering the material to your site, especially for larger projects or if the site is difficult to access.
- Labor Costs: If you’re hiring workers, the cost of labor can add significantly to your overall budget. Rates vary by region and the complexity of the job.
- Pumping Fees: For projects where the concrete needs to be pumped to hard-to-reach areas, such as high-rise buildings or areas with restricted access, additional pumping fees may apply.
- Finishes: Stamped or decorative concrete finishes can enhance the appearance of your project but come with added costs. These include not only the cost of materials but also skilled labor for installation.
Each of these expenses should be carefully considered to avoid any last-minute surprises. Be sure to get quotes from multiple suppliers and contractors to ensure you’re getting the best deal.
DIY vs. Hiring a Contractor
One of the biggest decisions you’ll need to make is whether to take a DIY approach or hire a professional contractor. Both options have their pros and cons, and the right choice will depend on your budget, the complexity of the project, and your level of experience.
DIY Approach
Pros
- Lower Costs: The most obvious advantage of a DIY approach is saving on labor costs. You only pay for materials, equipment rental, and possibly some extra help.
- Flexibility: You can work on your schedule and pace, adjusting as needed.
Cons
- Time and Effort: Concrete work is labor-intensive, especially for larger projects. It can take a lot of time and effort if you’re inexperienced.
- Equipment Rental: You’ll likely need to rent equipment like concrete mixers, wheelbarrows, and finishing tools, which can add to the costs.
- Quality Risk: Without proper knowledge and technique, the final result may not be as polished or durable as a professionally installed slab.
Hiring a Contractor
Pros
- Professional Quality: A contractor brings experience, skill, and specialized equipment, ensuring that the job is done correctly and efficiently.
- Time Efficiency: Professionals can complete the job in a fraction of the time it might take for a DIY project.
- Warranty and Accountability: Reputable contractors often offer a warranty on their work, providing peace of mind.
Cons
- Higher Costs: Hiring a contractor will increase your overall project cost due to labor charges, but the added expertise might be worth the investment for a larger or more complex project.
Accurately calculating the total concrete cost for your project requires careful planning and attention to detail. By following these steps, you can estimate your material needs, factor in additional costs, and decide whether to handle the project yourself or hire a contractor. This will help you budget effectively and ensure that your concrete project goes smoothly, from start to finish. If you’re ever in doubt, don’t hesitate to consult a professional for advice and to obtain quotes tailored to your specific needs. By doing so, you can make informed decisions and avoid unexpected costs down the road.
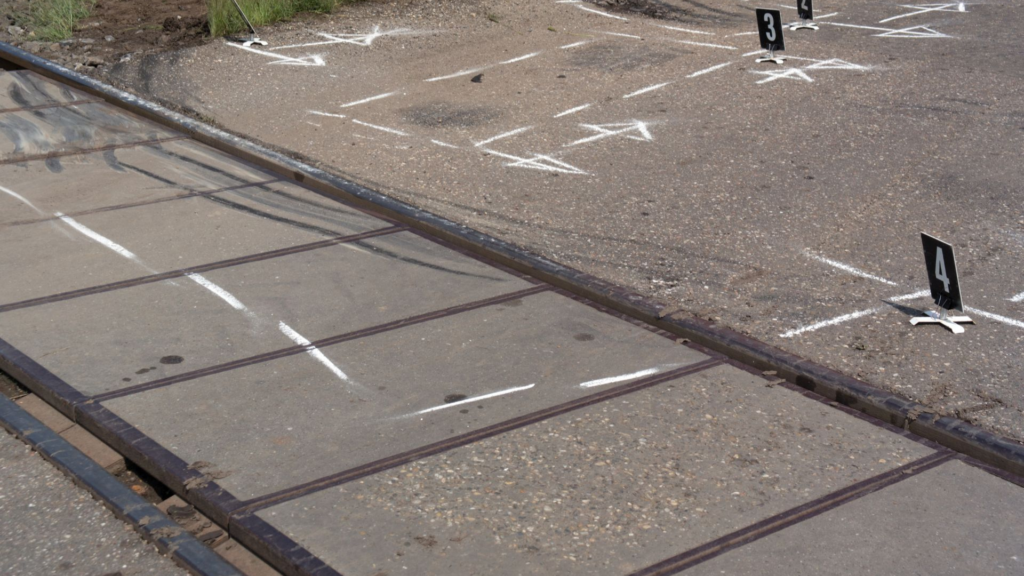
DIY Vs. Hiring A Contractor
When tackling a concrete project, whether for a driveway, patio, or small garden pathway, the question of whether to go the DIY route or hire a professional contractor is an important one. Both options have their own advantages and drawbacks, and the decision ultimately depends on the project’s complexity, budget, and your skill level. Let’s break down the pros and cons of DIY concrete projects versus hiring a contractor, along with cost considerations to help you make an informed choice.
The Pros and Cons of DIY Concrete Projects
For homeowners who enjoy hands-on work, doing a concrete project yourself can seem like a fun and rewarding challenge. However, it’s important to consider both the benefits and drawbacks.
Renting Tools, Sourcing Materials, and Labor Involved
One of the primary motivations for DIY is cost savings. At first glance, doing it yourself seems cheaper since you’re not paying for labor. But, let’s take a closer look at the specific costs involved.
- Renting tools: You’ll need specialized equipment such as a concrete mixer, trowels, and finishing tools. The cost of renting these tools can add up, ranging from $100 to $300+ per day, depending on the type and size of the equipment.
- Sourcing materials: You’ll have to purchase concrete mix, rebar, wooden forms, and other materials. Concrete is typically sold by the cubic meter, and depending on your project size, this cost can range between $150 to $200 per cubic meter in New Zealand.
- Labor: While you’re saving on contractor fees, don’t forget the labor is now your responsibility. Mixing, pouring, leveling, and finishing concrete is physically demanding and time-consuming work, and you’ll likely need extra hands for large pours.
For small projects, such as a garden walkway or a small patio, DIY can be cost-effective if you already own some tools and have the time and energy to invest. However, the true cost of DIY often comes in the form of unforeseen mistakes, extra time spent, and potential quality issues that can cost more to fix later.
Realistic Expectations for DIY Concrete Projects
DIY concrete projects are often more suited for smaller, less complex jobs. For example, pouring a small slab for a shed or creating a simple garden pathway can be manageable if you’re willing to put in the effort. However, when it comes to larger, more intricate projects like driveways, garage floors, or anything requiring a significant volume of concrete, things can quickly become overwhelming.
Concrete pouring has to be done quickly and accurately, as the material sets fast. If you misjudge your timing or get the mix wrong, you might end up with cracks, uneven surfaces, or structural issues that will cost you more to fix in the long run. Furthermore, achieving a smooth and professional finish requires skill and experience that DIY enthusiasts may not have.
The Benefits of Hiring a Professional Contractor
If you’re looking for a hassle-free experience with quality results, hiring a professional concrete contractor is usually the better option, especially for larger or more intricate projects. Here are the key benefits:
Peace of Mind
Hiring a contractor brings peace of mind. You can rest assured that the job will be done correctly, safely, and within building codes. A professional will handle everything from site preparation to pouring and finishing, reducing the risk of mistakes. Plus, most contractors offer guarantees for their work, so if any issues arise later, you’re covered.
Quality of Work
Concrete work requires precision. From getting the correct concrete mix to leveling and curing, the smallest mistakes can lead to long-term problems like cracking or sinking. Professionals bring experience and expertise, ensuring a high-quality finish that will last for years without needing repairs.
Long-Term Savings
While hiring a contractor might seem like a higher upfront cost, it can actually save you money in the long term. A professional will complete the project efficiently and correctly the first time, minimizing the risk of costly mistakes. In contrast, DIY projects, especially those done with less experience, often result in repairs or replacements down the road, negating any initial savings.
Cost Estimates for Hiring a Contractor in New Zealand
The cost of hiring a contractor in New Zealand varies depending on the scope of the project, materials used, and your location. On average, you can expect to pay between $60 to $100 per hour for labor. Here’s a general breakdown of what you can expect.
- Small projects: For a simple job like pouring a small concrete slab or pathway, you might spend between $1,500 and $3,000, including materials and labor.
- Medium projects: A mid-sized project like a driveway or patio could cost anywhere from $4,000 to $10,000, depending on the size and complexity.
- Large projects: Larger undertakings like a concrete garage floor or a sizable driveway can cost upwards of $15,000 or more.
Additionally, professional contractors often provide project management, ensuring that everything from sourcing materials to coordinating work schedules runs smoothly. This service can be invaluable if you’re looking to avoid the stress of managing a construction project on your own.
When deciding between DIY and hiring a contractor for your concrete project, it’s essential to weigh the costs and benefits. If you’re working on a small project, have the necessary tools, and feel confident in your abilities, going the DIY route could save you some money. However, for larger or more complex jobs, hiring a professional contractor ensures quality, peace of mind, and long-term savings. Though the upfront cost may be higher, the reduction in potential mistakes and future repairs often makes it the more cost-effective choice in the long run. By understanding the full scope of what’s involved, you can make the decision that best fits your needs, budget, and skill level.
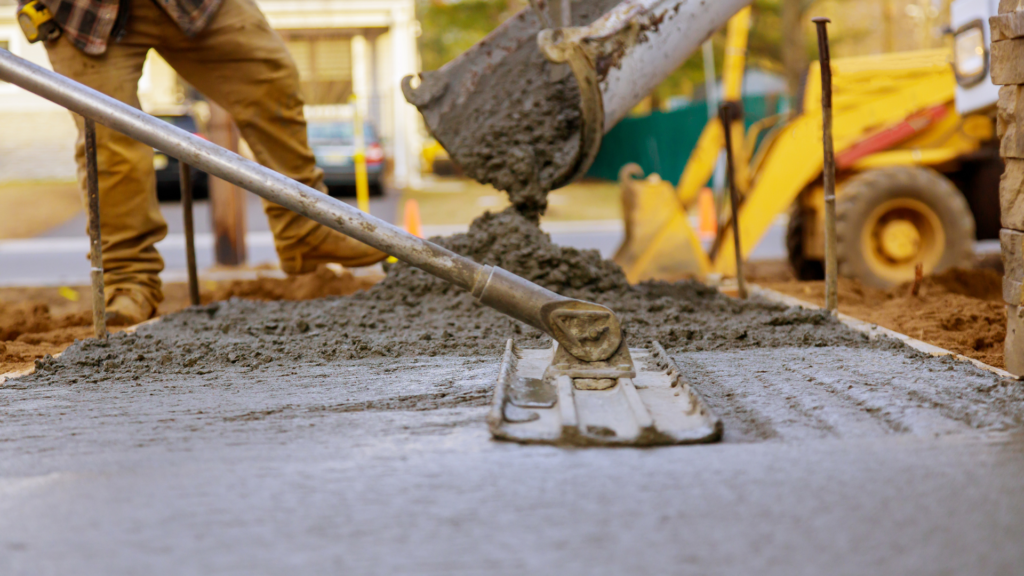
Tips For Getting The Best Value For Your Concrete Purchase
When it comes to buying concrete, there are several smart strategies you can use to make sure you’re getting the best bang for your buck. Whether you’re working on a large-scale project or a few smaller jobs, following these tips will help you save money and avoid potential headaches.
Buy in Bulk for Larger Projects
One of the easiest ways to save money on concrete is by purchasing in larger volumes. If you’re tackling a big project or even multiple smaller projects, ordering concrete in bulk can significantly reduce the overall cost per unit. Many suppliers offer discounts when you buy in larger quantities, helping you cut down on delivery fees and minimize wastage. If you have a few smaller projects lined up, consider bundling your orders together to take advantage of these savings. This can be especially helpful if you expect to need more concrete in the near future, as it helps you lock in a price and avoid potential price increases down the line.
Plan and Order Ahead
Timing is crucial when it comes to getting the best value for your concrete purchase. Planning your project in advance and ordering your concrete ahead of time can help you avoid rush fees or delivery delays. Last-minute orders often come with higher prices, especially if the supplier has to make special arrangements to accommodate you. By scheduling your delivery well in advance, you ensure that the concrete arrives when you need it without any extra charges. Plus, you’ll have more flexibility in choosing the best supplier for your needs, as you won’t be stuck with whoever can deliver on short notice.
Negotiate and Shop Around
Concrete prices can vary widely depending on the supplier, so it pays to shop around. Don’t be afraid to ask for a better deal, especially if you’re placing a larger order. Some suppliers are willing to offer discounts or special pricing for bulk orders, repeat customers, or even based on the time of year. It’s always worth negotiating – even if a supplier doesn’t lower the price, they might offer additional perks like reduced delivery fees or flexible payment terms. Comparing quotes from multiple suppliers ensures you get the most competitive price and best overall value.
Ask for Local Recommendations
Local recommendations are often a hidden gem when it comes to finding great deals on concrete. Neighbors, builders, or community groups may already have experience with reliable suppliers in your area, and they can point you in the direction of a trustworthy company that offers good prices. Local suppliers may also be more flexible when it comes to delivery times or willing to negotiate on price, especially if they know you’re part of the local community. Additionally, choosing a local supplier helps reduce transportation costs, which can sometimes be a significant part of the overall price, especially for larger orders.
By keeping these tips in mind, you can ensure that you’re making a smart, cost-effective choice when purchasing concrete for your next project. Whether you’re saving through bulk buying, careful planning, or negotiating a deal, these strategies will help you get the best value for your concrete investment.
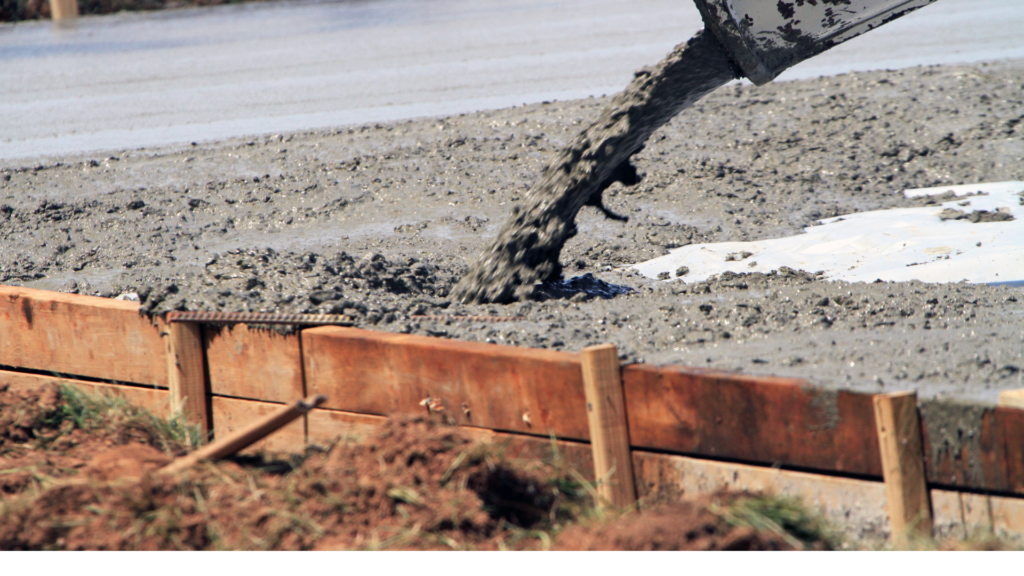
FAQs: About Concrete Price Per M³ NZ
Conclusion
Understanding the various factors that influence concrete prices in New Zealand is essential for anyone planning a construction project. From the type of concrete mix selected to additional costs like delivery fees, labor, and potential waste management, every aspect can significantly impact your overall budget. Being aware of these details enables you to make more informed decisions, ensuring that you choose the right materials and services for your specific needs. By calculating the exact volume of concrete required, you can avoid overspending and reduce wastage, which can further optimize your costs. It’s crucial to reach out to local suppliers to get quotes tailored to your project’s specifications, ensuring that you’re not only comparing prices but also understanding the value of quality service and materials. With the insights gained from this blog, you are now better equipped to plan and execute your project efficiently. Take action today by using this knowledge to kickstart your project, getting the best possible value for your investment while ensuring a smooth and successful construction process.
About the Author:
Mike Veail is a recognized digital marketing expert with over 6 years of experience in helping tradespeople and small businesses thrive online. A former quantity surveyor, Mike combines deep industry knowledge with hands-on expertise in SEO and Google Ads. His marketing strategies are tailored to the specific needs of the trades sector, helping businesses increase visibility and generate more leads through proven, ethical methods.
Mike has successfully partnered with numerous companies, establishing a track record of delivering measurable results. His work has been featured across various platforms that showcase his expertise in lead generation and online marketing for the trades sector.
Learn more about Mike's experience and services at https://theleadguy.online or follow him on social media: